Understanding the Costs of Electric Car Manufacturing
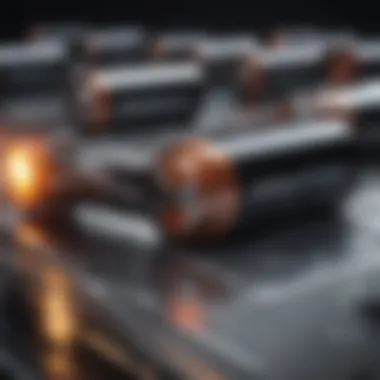
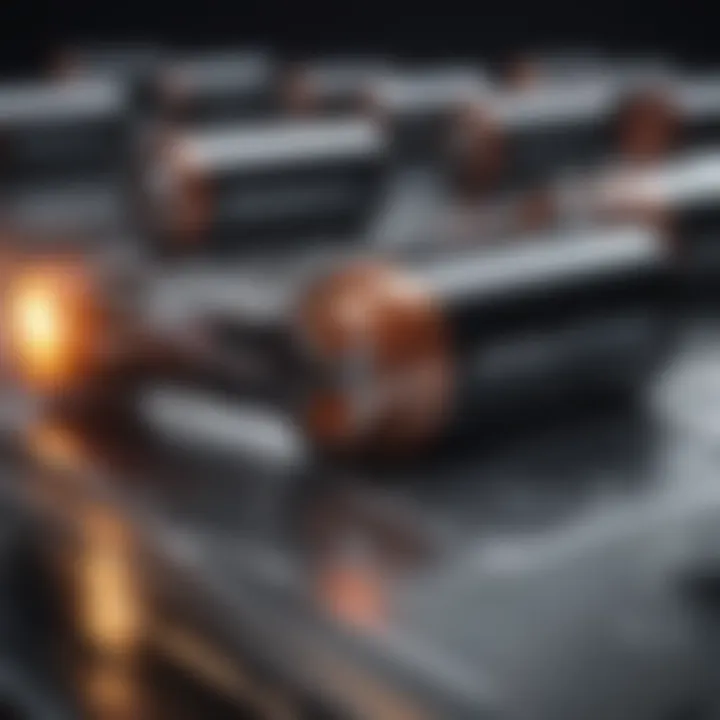
Intro
The electric vehicle market is growing rapidly, and with it, the complexity of its manufacturing process. There's more to creating these innovative machines than meets the eye. From the intricate dance between technology and economics, to understanding where all the costs pile up, this article seeks to untangle the threads of electric car manufacturing.
If you’re looking to make sense of what drives expenses in this field, you’ve hit the jackpot. We will journey through key components of production, labor inputs, and the advancements in technology that can pinch or save pennies. Each element plays a vital role in how much it takes to put an electric vehicle on the road.
Beyond just looking at figures, we’ll also chat about the influence of battery technology, regulatory pressures, and the sometimes messy web of the supply chain. By the end of this exploration, whether you are an investor thinking about diving into this industry or merely someone curious about the future of transport, you will gain a clear understanding of the financial dynamics at play in the electric car world.
Overview of Electric Vehicle Manufacturing Costs
Electric vehicles (EVs) have surged into the limelight in recent years, as the world trends toward sustainability and eco-friendly technologies. This shift also brings to the forefront the costs associated with manufacturing electric vehicles. Understanding these costs is crucial not just for manufacturers but also for investors and enthusiasts who follow the industry closely. As we dissect this topic, we will explore the various elements driving these expenses and how they interconnect.
Prelude to Cost Structure
The cost structure of electric vehicle production is multifaceted, encompassing a range of components from raw materials to labor expenditures and everything in between. Each of these elements plays a pivotal role in the overall price tag associated with electric cars. For instance, the pricing of battery systems—a major element in EV costs—can significantly affect overall expenses. As lithium and cobalt prices fluctuate, so too do the costs of producing electric vehicles.
In addition to materials, the intricacies of labor costs also weigh in on the final product price. Skilled labor is often required for assembly and integration of advanced technologies utilized in EV manufacturing. Furthermore, companies need to consider overhead costs, including research and development, which are essential for innovating and staying competitive.
Overall, the importance of dissecting cost structures lies in the ability to make informed decisions. Investors seeking opportunities in the EV market should fully grasp what influences these costs, paving the way for profitable engagements in the industry.
Comparative Analysis with Conventional Vehicles
When drawing comparisons between electric vehicles and conventional combustion vehicles, the differences in manufacturing costs become apparent. Traditional cars have a simpler mechanical structure, which often translates to lower production costs. However, the rapid advancements in technology for EVs are beginning to narrow this gap.
For example, while gasoline-powered cars require extensive exhaust systems and components that add to manufacturing complexity, electric vehicles rely heavily on battery systems and electric drivetrains. This shift can lead to substantial changes in cost dynamics, often making electric cars more expensive to produce initially, yet potentially offering long-term savings in maintenance and fuel.
Moreover, with the market's growth, economies of scale could come into play. As more manufacturers transition to electric vehicles, mass production could help drive down costs significantly, benefiting consumers.
"The shift towards electric vehicles is not merely a trend but a significant change in how we perceive mobility and the associated costs."
In summary, the comparative analysis between electric and conventional vehicle costs highlights important trends and considerations for the future. Both production methodologies have their advantages and challenges, and understanding these nuances will undoubtedly shape the strategies of industry stakeholders as they navigate this evolving landscape.
Key Components Driving Manufacturing Expenses
Understanding the costs tied to the manufacturing of electric vehicles centers on several pivotal components, each influencing the bottom line significantly. These elements not only dictate the initial investment but also shape the long-term price structure of electric cars. Manufacturers need to balance innovation and cost-effectiveness to appeal to both investors and consumers alike. Here, we will delve into three critical areas: battery systems, electric motors, and chassis design.
Battery Systems and Their Costs
Batteries are the heart of any electric vehicle, serving as the main power source. The cost of battery systems generally comprises materials, manufacturing processes, and R&D investments. For instance, lithium-ion batteries, which have become the industry standard, incur hefty price tags due to lithium, cobalt, and nickel sourcing complexities. These materials are often mined in regions with unstable political climates, which can rack up the costs due to logistics and supply chain issues.
The recent trend is moving towards developing solid-state batteries, which could promise far greater energy density and safety. However, the shift involves enormous costs in both development and production. With developments like Tesla’s plans for a Gigafactory, the aim is to lower battery costs by producing on a larger scale, allowing for economies of scale to kick in.
Moreover, the overall battery costs are often reflected in the final price of an electric vehicle, making this component a critical area of focus for manufacturers looking to remain competitive in the market.
"The battery is not just another component; it is arguably the most decisive factor in determining the future of electric vehicle technology."
Electric Motors and Power Electronics
Electric motors drive the performance of electric vehicles. They convert electrical energy into mechanical energy, which propels the car forward. Despite having fewer moving parts than traditional internal combustion engines, electric motors can still be costly. Production expenses for these motors stem from raw materials like rare earth magnets, precision engineering, and assembly processes.
Power electronics too play a vital role, ensuring the vehicle operates efficiently. This segment includes components like inverters and converters, which are cars’ brains managing the flow of electricity. The collective costs of electric motors and power electronics make up a significant portion of the vehicle’s overall manufacturing expenditure.
Chassis and Body Design Considerations
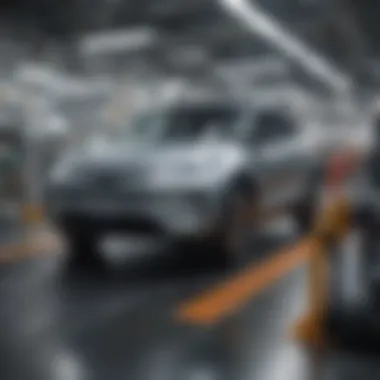
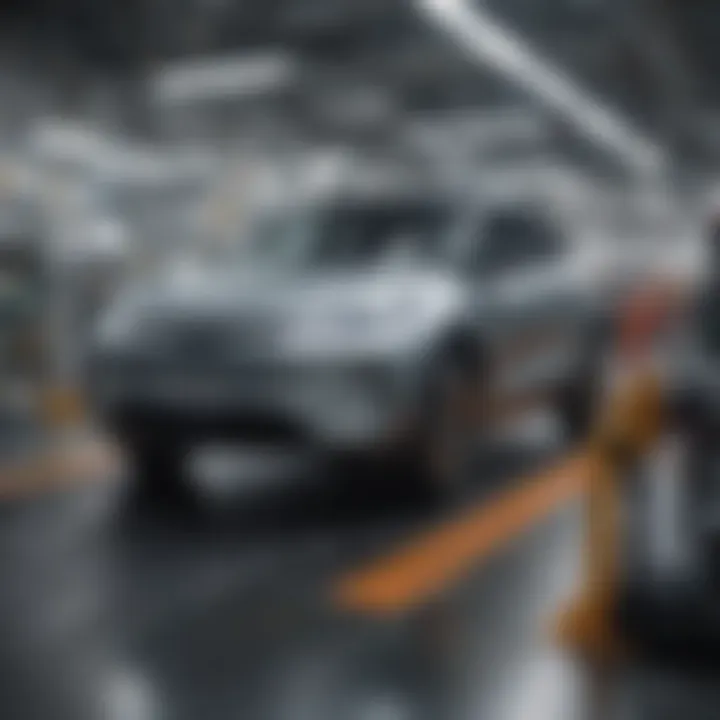
The chassis and body design make up the skeletal structure of the vehicle. A well-constructed chassis contributes not only to the vehicle's stability and durability but also actively impacts efficiency. Considerations such as weight reduction are vital. Materials like aluminum and composites may be more expensive but offer significant weight savings, which directly enhances battery performance and range.
Structural integrity is also a priority. Manufacturers face the challenge of creating lightweight designs without compromising safety standards. Innovations like multi-material construction have emerged as solutions, but they often come with higher production costs due to complex welding and assembly techniques.
In summary, focusing on the key components driving manufacturing expenses is crucial for understanding the economic landscape of electric car production. By scrutinizing battery systems, electric motors, and chassis designs, stakeholders can better navigate the intricate world of electric vehicle manufacturing costs, making informed decisions that contribute to ongoing advancements in the electric vehicle domain.
Labor Costs in Electric Car Production
Labor costs play a pivotal role in electric car production. As the industry evolves, understanding this aspect becomes increasingly important for investors and enthusiasts alike. While material costs often grab headlines, labor expenditures can significantly shape the overall financial landscape of electric vehicle manufacturing. The people behind the scenes, from assembly line workers to engineers, not only contribute to the quality of the product but also directly impact the economic viability of a manufacturing enterprise.
As electric vehicles (EVs) incorporate advanced technology and components, the demand for skilled labor rises. This need for expertise may influence pricing structures and dictate where companies choose to establish their production facilities. Navigating labor market dynamics is essential for predicting future trends in the costs associated with electric vehicle manufacturing.
Overview of Labor Market Dynamics
The labor market in the electric car sector can be considered a dynamic entity, heavily influenced by technological advancements, global competition, and shifts in consumer behavior. Factors such as regional economic conditions and educational infrastructure also affect the availability of skilled workers.
- Skill Gaps: As electric vehicles become more sophisticated, the requirement for skilled labor grows. Many traditional automotive workers may not possess the necessary skills for electric vehicle production, creating a skill gap.
- Wage Trends: It's worth noting that wages for skilled labor in the EV market are typically higher than those in conventional vehicle production. This is mainly due to the specialized knowledge and training required. Companies may find themselves in bidding wars for the best talent, further driving up personnel costs.
- Geographical Factors: For companies, the choice of location affects labor costs. Areas with high unemployment might offer lower wages, but the availability of skilled workers becomes a crucial consideration in site selection. Conversely, regions with a skilled workforce might demand higher salaries, impacting overall expenses.
"Understanding labor dynamics is key to successfully navigating the manufacturing landscape of electric vehicles. Without a grasp of the workforce trends, companies risk falling behind their competitors."
Skilled Labor vs. Automation
The balance between skilled labor and automation is a double-edged sword in electric car production. On one hand, automation promises to reduce labor costs and enhance production efficiency. On the other, the need for skilled labor remains undeniable, particularly for complex tasks that machines cannot easily replicate.
- Rise of Automation: Automation technologies such as robotics have made significant inroads into the manufacturing process. They can perform repetitive tasks quickly and with precision. For instance, robots can effectively handle welding and painting, which are both labor-intensive and time-consuming when done manually.
- Human Touch: Despite the benefits of technology, there are areas where human oversight and decision-making are irreplaceable. Skilled personnel are essential for monitoring processes, troubleshooting equipment, and ensuring quality control.
- Cost Analysis: The upfront investment for automation can be substantial, but when viewed over the long term, these technologies can decrease labor costs significantly. Yet, companies must also consider the ongoing costs of maintenance, software updates, and training for their existing workforce to handle new technologies.
Technological Innovations Impacting Costs
Technological innovations play a pivotal role in shaping the costs associated with manufacturing electric vehicles. These advancements have the potential to significantly reduce expenses while enhancing performance and sustainability. As the industry rapidly evolves, understanding how these innovations affect costs is crucial for stakeholders looking to navigate the complexities of electric vehicle production.
Advancements in Battery Technology
One of the most significant factors influencing the manufacturing costs of electric vehicles is battery technology. Over the last decade, there has been a tremendous push towards more efficient, lightweight, and cost-effective battery solutions. The lithium-ion battery remains the gold standard in EVs, but ongoing research into alternatives, such as solid-state batteries and lithium-sulfur variations, holds promise.
"Battery power is not just about the charge; it's about the charge's cost and how quickly it gets you there."
These innovations help lower costs for manufacturers in several ways:
- Increased Density: Newer battery technologies manage to pack more energy into less space. This leads to lighter and smaller power units, trimming excess material costs.
- Faster Charging: Advancements in charging technology can cut down charging times, allowing manufacturers to utilize production lines more efficiently.
- Longer Lifespan: Batteries that can withstand more charge cycles reduce the need for replacements, ultimately decreasing long-term ownership costs for consumers.
Such factors not only impact the bottom line directly but also improve consumer attractiveness towards electric vehicles, influencing purchasing decisions.
3D Printing and Its Role in Manufacturing
Another groundbreaking innovation is the rise of 3D printing in the automotive industry. This technology is not just a catchy buzzword; it’s revolutionizing the way components are designed and produced. 3D printing allows for:
- Rapid Prototyping: Engineers can quickly create prototypes, test them, and modify designs, which both speeds up the production process and reduces costs linked to conventional prototype manufacturing.
- Custom Components: Manufacturers can produce tailored parts without the need for large-scale molds, which are often costly and time-consuming.
- Material Efficiency: 3D printing generally uses only the materials necessary to create a part, minimizing waste.
As electric vehicle manufacturers embrace 3D printing, the implications for cost reduction become clear: less material waste, quicker turnarounds, and improved supply chain dynamics. The ability to print components on-demand means production can be more adaptable to shifts in consumer demand, reducing the costs tied to overproduction.
Overall, as electric vehicle production integrates advanced technologies like battery innovations and 3D printing, costs are likely to lessen. This trend can lead to lower retail prices for consumers while also making the manufacturing processes more sustainable and efficient.
Supply Chain Considerations
Understanding the complexities of the supply chain in electric vehicle (EV) manufacturing is critical. The supply chain affects everything from production timelines to final product pricing, profoundly influencing how smoothly a company can operate. In an industry that is rapidly expanding and innovating, supply chain efficiency can be a major differentiator in keeping manufacturing costs manageable.
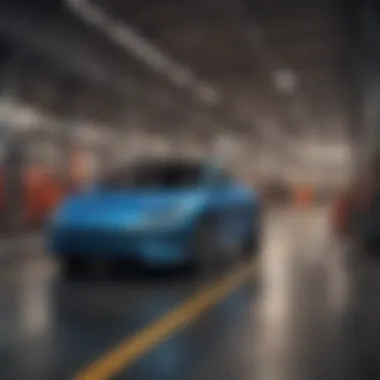
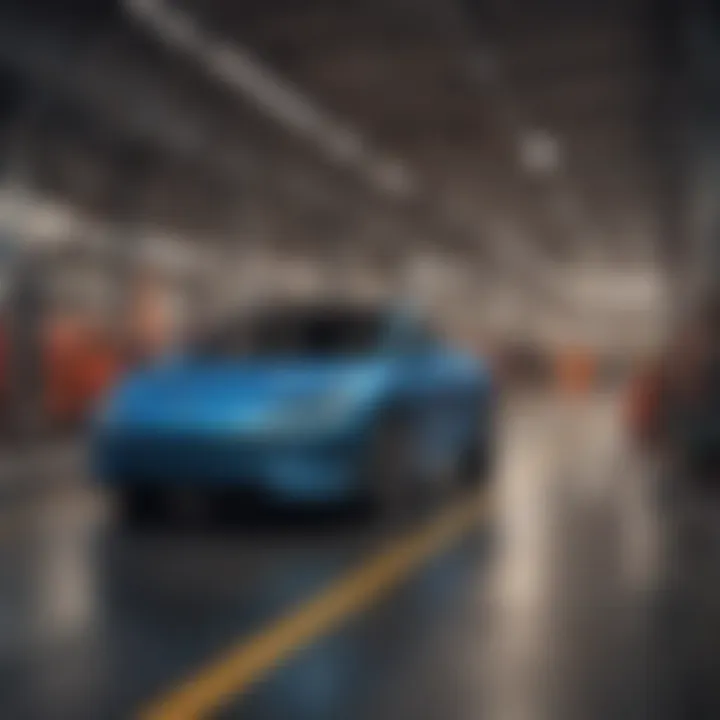
Raw Material Sourcing Challenges
The raw materials used in electric vehicles, particularly lithium, cobalt, and nickel for batteries, present significant sourcing challenges. According to the International Energy Agency, the demand for lithium alone is expected to soar, influenced by the surge in EV adoption. This puts pressure not just on suppliers but on manufacturers to secure their materials.
- Scarcity: The minerals essential for battery production are increasingly harder to come by. Conflicts in mining regions and intricate geopolitical landscapes can significantly affect access.
- Price Volatility: Fluctuations in commodity prices can make budget forecasting problematic. A sudden spike in cobalt prices, for instance, can lead to a substantial increase in production costs, which must be addressed to maintain profit margins.
- Sustainability and Ethics: There is growing scrutiny on the sourcing methods of these materials. Manufacturers face pressure to ensure that their supply chains are ethically sound, forcing many to invest in audits or certifications.
These factors require companies to build resilient sourcing strategies and perhaps even explore alternatives, such as recycling materials, to alleviate pressures on the supply chain.
Global Supply Chain Vulnerabilities
In the globalized market, vulnerabilities in the supply chain can have a ripple effect. Events such as natural disasters, trade disputes, or economic sanctions can disrupt the flow of essential materials. For instance, the COVID-19 pandemic exposed weaknesses in global supply chains, highlighting how reliant manufacturers are on various international suppliers.
- Single Source Dependence: Relying on a single country or supplier for critical materials can be risky. A sudden trade embargo or political instability can halt production lines, leading to delays and financial losses.
- Transportation Hurdles: The logistics of transporting materials across continents adds complexity. Inefficiencies in shipping and handling can result in increased costs and longer lead times, which can be detrimental to just-in-time manufacturing operations.
- Technological Disruptions: Cybersecurity issues have emerged as another threat. Supply chain attacks can compromise systems that manage sourcing and logistics, leading to data breaches and operational disruptions.
The fragility of global supply chains has prompted manufacturers to consider reshoring or diversifying their supply networks as a countermeasure.
Regulatory Factors Influencing Costs
The landscape for electric vehicle (EV) manufacturing is not just shaped by technological advancements and material expenses. It’s also significantly molded by regulatory influences. Regulatory factors can create both roadblocks and pathways in manufacturing costs. They impact how companies structure their processes, which can lead to notable variations in overall expenditure based on compliance and incentives. Over time, understanding these dynamics becomes essential for investors and industry players alike, as they cradle the financial future of electric mobility.
Government Subsidies and Incentives
One of the more favorable aspects of the regulatory environment is government subsidies. These financial incentives can ease a manufacturer’s burden by providing monetary support for research, development, and production. For instance, the U.S. government has offered tax credits for consumers purchasing electric cars, boosting demand and effectively lowering the costs spread across production.
This type of support can channel resources into innovative areas, such as advancing battery technology and enhancing manufacturing efficiency. In places like Europe, various countries offer their own incentives, which can include direct subsidies for manufacturers who meet green standards. These initiatives not only make production viable but also help maintain competitive pricing against traditional gas-powered vehicles.
However, the downside is that these incentives are frequently under review. Changes in political mood can alter the level of support provided, sparking unpredictability. For manufacturers, this means staying agile—developing strategies to navigate the aftermath should subsidies be reduced or eliminated altogether.
Environmental Regulations and Compliance Costs
While incentives can lower costs, environmental regulations often serve as a double-edged sword. The push toward sustainable practices can lead to increased compliance costs for electric vehicle makers. These regulations mandate specific standards for emissions, waste management, and energy use, all of which require investment in cleaner technologies and manufacturing methods.
For example, the European Union has implemented strict emissions standards. Meeting these can lead to significant cost implications. Often, manufacturers must invest in new technologies or processes to align with these stringent requirements. Although the investments may be hefty upfront, they could yield savings over time through reduced resource consumption. This ongoing commitment to compliance creates a balance in cost consideration—striking while the iron is hot in terms of both investment and long-term sustainability.
The interplay of these regulatory factors creates a complex cost environment. To sum up, the influence of government support and environmental regulations presents both advantages and challenges. EV manufacturers must consistently monitor these dynamics to adapt to the ever-changing landscape.
"Predicting regulatory changes is akin to forecasting the weather; it can be unpredictable, yet it’s a necessity for manufacturers in this evolving industry."
Economies of Scale in Production
As electric vehicle manufacturing accelerates, the concept of economies of scale becomes pivotal. In essence, economies of scale refer to the cost advantages that firms obtain due to the scale of their production, which leads to a reduction in per-unit costs. This phenomenon is particularly crucial for electric vehicle makers who are navigating a landscape often characterized by high initial investments and intense competition.
When a company ramps up its production, fixed costs such as plant maintenance, salaries for management staff, and equipment depreciation are distributed over a larger number of units produced. This capacity allows manufacturers to lower the cost per vehicle significantly. A practical example can be seen with Tesla. By increasing production rates, Tesla has managed to reduce the production costs per vehicle, which in turn supports its pricing strategy and market reach.
Benefits of Achieving Economies of Scale:
- Lower Per Unit Costs: As more vehicles are produced, the overhead spreads thin, reducing costs.
- Enhanced Bargaining Power: Larger manufacturers often hold more sway over suppliers, leading to discounts on raw materials.
- Investment in Technology: Companies with higher volumes can allocate more funds to research and development, fostering innovation.
- Market Positioning: Lower costs can enable aggressive pricing, enhancing market penetration and competitive advantage.
While there are notable benefits, achieving economies of scale isn't without its challenges. Oversaturation of the market or miscalculating demand can lead to excess inventory, thus countering the benefits. Manufacturers must balance scaling production with market trends to avoid costly pitfalls, which could eventually impact profitability.
How Scale Reduces Unit Costs
When it comes to unit cost reductions, scale plays a central role. Imagine a bakery that makes 50 loaves of bread daily versus one that produces 5,000. The larger bakery can buy ingredients in bulk, reducing the overall cost per loaf. In the same vein, electric vehicle manufacturers experience similar dynamics.
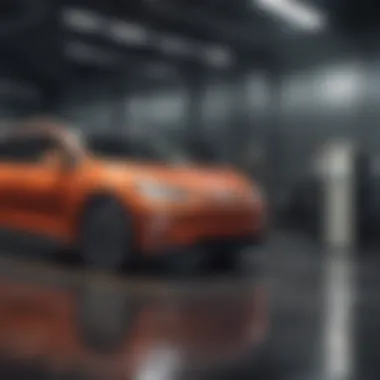
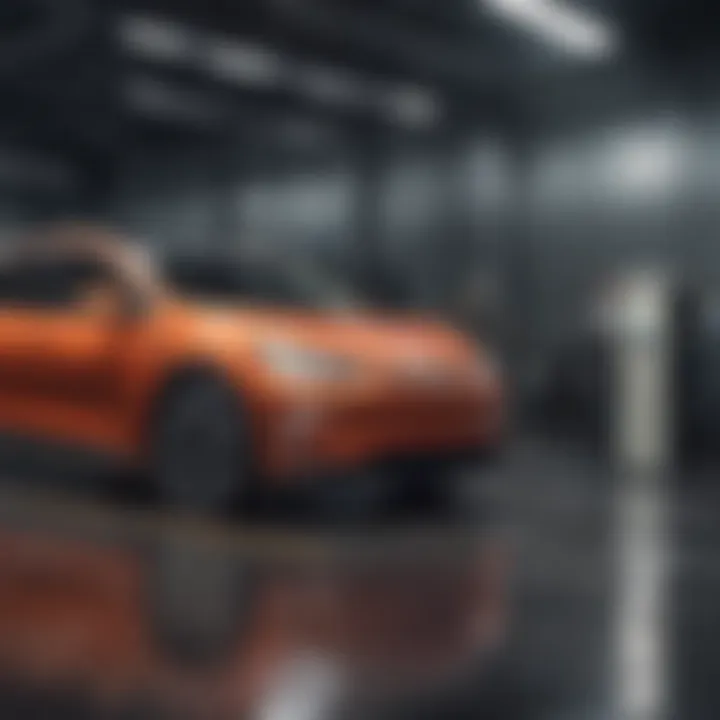
Factors Contributing to Cost Reduction:
- Bulk Purchasing: Large-scale producers can negotiate lower prices for raw materials like lithium, cobalt, and aluminum used in battery production, driving down material costs.
- Specialization of Labor: As production increases, companies can hire skilled labor for specific tasks, improving efficiency and reducing labor costs over time.
- Streamlined Processes: High-volume production allows for the refinement and streamlining of manufacturing processes. This results in less waste and higher efficiency.
- Technological Advancements: With more resources at their disposal, manufacturers can invest in cutting-edge technologies like automation, further driving down costs.
Essentially, the relationship between scale and unit costs creates a cumulative effect. As production increases, the cost curve bends downwards, making electric vehicles more economically viable.
Case Studies on High-Volume Manufacturers
Exploring the success stories of high-volume manufacturers provides valuable insights into how economies of scale positively impact costs.
- Tesla: A leading player in the electric vehicle sector, Tesla has continuously increased its production rate over the years. Their Gigafactories are designed to produce batteries at an unprecedented rate, significantly lowering their costs. Tesla's ability to produce over a million vehicles annually not only reduces unit costs but also keeps them competitively priced in the market.
- Volkswagen: Volkswagens commitment to EVs is another case in point. The brand plans to manufacture 1.5 million electric vehicles annually by 2025. Such scalability enables them to leverage their existing supply chains effectively, allowing for negotiation power and lowering production costs per unit.
- Nissan: With the Nissan Leaf being one of the highest-selling electric vehicles globally, Nissan illustrates how investing in mass production facilities results in reduced costs. By producing nationally in key markets, administrators can streamline logistics and reduce transport expenses.
These case studies underline that operating at higher volumes leads to lower costs, which ultimately shapes the landscape of electric vehicle manufacturing.
"In the world of electric vehicle manufacturing, the key to remaining competitive lies within the ability to reduce costs through economies of scale."
Future Trends in Electric Vehicle Manufacturing Costs
The electric vehicle (EV) industry is at a crossroads, teetering between rapid technological advancements and evolving consumer preferences. Understanding the future trends in electric vehicle manufacturing costs is essential not only for manufacturers but also for investors and stakeholders interested in this burgeoning sector. Forecasting these trends helps in discerning potential market opportunities, assessing risk factors, and optimizing investment strategies.
In this section, we’ll dissect the predictions regarding technology evolution and analyze how shifts in consumer demand will shape the costs associated with manufacturing electric cars. The objective here is to offer a nuanced perspective that can inform your decisions and strategies in an increasingly competitive landscape.
Predictions on Technology Evolution
Technology plays a pivotal role in reducing costs within the electric vehicle sector. Particularly, research and innovation surrounding battery systems, powertrains, and production methods are expected to drive down costs considerably over the next decade.
- Battery Innovations: The advent of advancements like solid-state batteries promises longer life spans and quicker charging times, effectively decreasing the overall cost of battery packs. This is significant as batteries make up a substantial portion of an EV's total cost. Improved battery recycling methods are also on the horizon, which could reduce the need for new raw materials, thus further helping the bottom line.
- Automation and Robotics: As automation becomes more sophisticated, factories will harness this technology to minimize labor expenses and improve precision. For instance, robotic arms that assemble battery packs will enhance efficiency and reduce human error. With the expected rise of smart manufacturing, companies can adapt their production processes in real-time to react to market demands.
- 3D Printing: This technology is poised to revolutionize parts manufacturing. By printing parts on demand, manufacturers can significantly cut inventory costs and waste. Additive manufacturing techniques will allow the creation of more complex geometries which often reduces weight, thereby improving the efficiency of the vehicle.
These innovations aren't just buzzwords; they imply concrete changes in the cost structures of electric vehicle manufacturing. The direct result will be more competitively priced and appealing electric vehicles to the consumer.
Shifts in Consumer Demand and Their Impact
Just as technology evolves, so does consumer behavior. The heightened awareness around climate change and sustainability has led many consumers to opt for electric vehicles. Here’s how these shifts in preferences are shaping production costs:
- Growing Demand for EVs: The increased consumer appetite for electric cars leads to volume production, which often results in economies of scale. When manufacturers can produce cars in larger quantities, the per-unit manufacturing cost typically decreases. This is a crucial factor; as demand increases, it incurs lower costs not just for manufacturers but also for consumers who retain the benefit of competitive pricing.
- Patient Buyers: Today's consumers want more than just lower costs; they are increasingly looking for features like improved battery life and advanced technology. This means manufacturers will need to balance costs with investments in R&D to meet these growing expectations. Failure to do so can lead to factory losses and unsold stock, impacting the overall financial health of companies.
- Second-hand Market Growth: As more electric vehicles hit the streets, a used market for these cars is likely to emerge. This could influence the pricing and demand for new EVs, allowing manufacturers to recalibrate their efforts in areas like sustainability and recycling. Furthermore, a robust market for used electric vehicles could alleviate some financial pressure on consumers, making first-time purchases more appealing.
"The electric vehicle market is not just about cars; it's about a shift in how we view transportation and sustainability. As technology advances and consumer demand shifts, those who adapt will thrive."
Understanding these factors can critically shape how you navigate the evolving world of electric vehicle investments.
Culmination
Understanding the costs involved in electric vehicle manufacturing is paramount for anyone looking to grasp the intricate dynamics of this rapidly evolving industry. As interest in electric vehicles continues to surge, manufacturers face a myriad of expenses that can deeply influence their market positioning. By evaluating these costs, we can better appreciate the strategic decisions manufacturers must make regarding technology investments, labor practices, and supply chain management.
The most notable elements at play include the significant investment in battery technology, which remains one of the highest costs associated with the production of electric cars. Additionally, as technological advancements unfold, manufacturers are tasked with integrating innovations that can lower these costs without compromising quality. Awareness of these factors is beneficial not only for investors seeking viable opportunities but also for consumers interested in the overall evolution of the automotive market.
Moreover, regulatory influences can add layers of complexity to manufacturing expenses. Depending on regional guidelines, compliance with environmental regulations or leveraging government incentives might shift cost structures dramatically.
As we continue to navigate this electrified era, recognizing the financial landscape will inform future choices and investments in electric vehicles. It serves both as a cautionary tale and a beacon of opportunity for those involved in or entering the market.
Key Takeaways
- Cost Structure Complexity: Electric vehicle manufacturing involves multi-faceted cost structures driven by technology, labor, and regulatory compliance.
- Battery Technology: The battery is a critical cost factor, representing a significant portion of manufacturing expenses. Innovations here could either alleviate or exacerbate costs.
- Supply Chain Challenges: Navigating raw material sourcing and global supply chain vulnerabilities is essential for managing costs efficiently.
- Regulatory Dynamics: Understanding the implications of governmental policies and environmental regulations can shift expected expenses and influence strategic decisions.
The Road Ahead for Electric Vehicle Manufacturers
The future of electric vehicle manufacturing promises to be an intriguing ride. As companies streamline their operations and economies of scale become more prevalent, we may witness a reduction in overall costs per vehicle produced. The dawn of new battery technologies—such as solid-state batteries—holds potential to drastically alter cost parameters, making electric vehicles more accessible to the average consumer.
Consumer demand will likely continue to evolve, with a growing focus on sustainability and efficiency. Manufacturers who adapt quickly to changing preferences will be at the forefront, while those who lag may find themselves unable to compete in a tightening market. This ever-changing landscape invites manufacturers to innovate relentlessly, whether through enhancing battery systems, refining supply chains, or exploring automation to reduce labor costs.
In summary, the electric vehicle market is far from static. By checking the pulse of technological and consumer trends, manufacturers can position themselves advantageously for the challenges and opportunities that lie ahead.